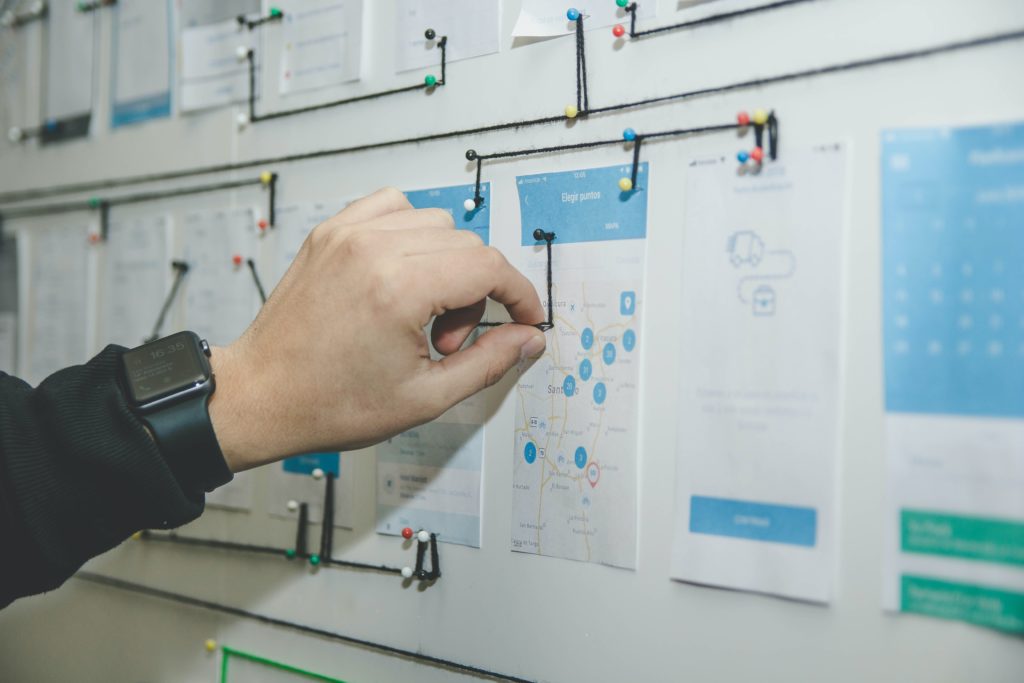
Process optimization is the practice of improving a particular process to enhance its efficiency and effectiveness. The ultimate goal of process optimization is to reduce waste, improve quality, and increase productivity in the organization. It is a continuous process that seeks to identify the best way to achieve a desired outcome while minimizing resource utilization. In this article, we will discuss why process optimization is important, its benefits, and the steps involved in the optimization process.
In the 1940s, process optimization evolved with the development of statistical process control (SPC). In the 1960s, the concept of total quality management (TQM) emerged. In the 1980s, it evolved again with the development of Lean manufacturing, pioneered by Toyota. In the 1990s, it became more data-driven with the development of Six Sigma using statistical analysis to measure and improve the quality of a process.
Today, process optimization is used in many industries beyond manufacturing. It has become a critical component of organizational improvement, with a focus on reducing waste, improving quality, increasing efficiency, and reducing costs.
Benefits of Process Optimization
Organizations strive to be efficient in all their operations. However, as the organization grows, it becomes increasingly difficult to manage all the processes manually. This is where process optimization comes in. Organizations adopt process optimization for a variety of reasons, some of which are listed below:
- Increase productivity: When a process is optimized, it takes less time to complete, thus increasing the number of tasks that can be completed in a given period.
- Improve quality: By identifying areas of a process that can be improved, organizations can improve the quality of their products or services. Improved quality leads to increased customer satisfaction, which ultimately translates to more business.
- Reduce costs: An optimized process reduces the cost of production by eliminating waste and improving efficiency. This allows organizations to reduce their operating costs and increase their profits.
- Remain competitive: Organizations that continuously optimize their processes can maintain their competitive edge in the market. This is because they can offer products or services at a lower cost and with better quality than their competitors.
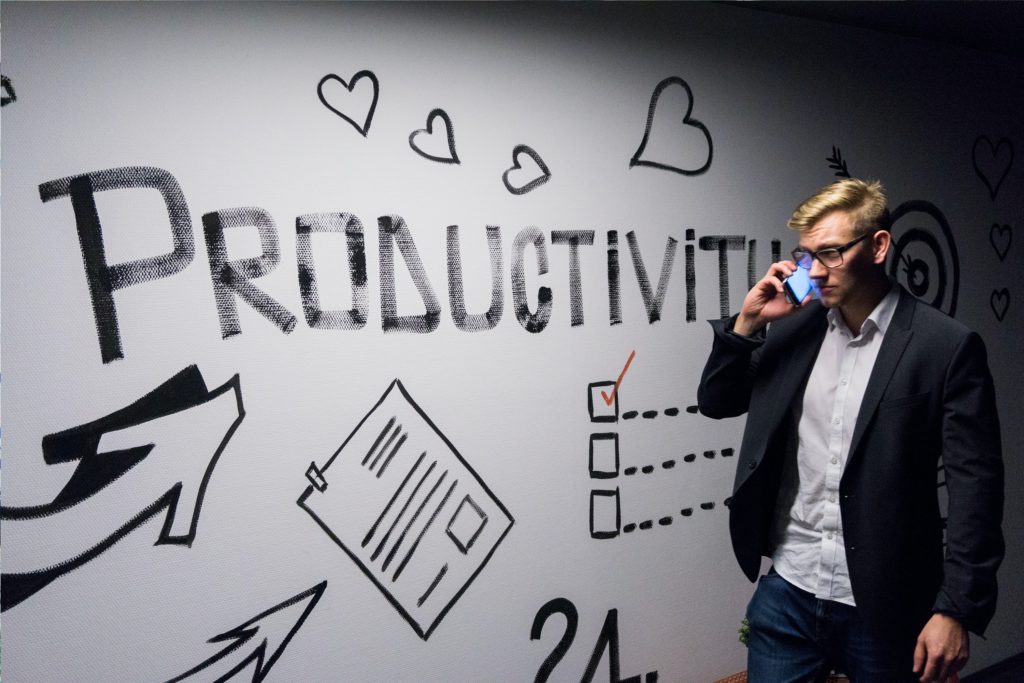
Steps in Optimizing a Process
- Identify the process: Identify the process that needs to be optimized. This involves defining the scope of the process, the inputs and outputs, and the stakeholders involved.
- Map the process: Documenting the steps involved in the process, the resources required, the decision points, and the handoffs.
- Analyze the process: This involves identifying bottlenecks, duplication, waste, and other inefficiencies. Various techniques can be used to analyze the process, including flowcharting, process mapping, and value stream mapping.
- Identify improvement opportunities: This involves brainstorming and prioritizing ideas to improve the process and are aligned with the organization’s strategic objectives.
- Implement improvements: This involves redesigning the process and implementing the changes. It is important to communicate the changes to all stakeholders and train them on the new process.
- Monitor and measure the process: Setting performance indicators and measuring the impact of the changes made. It is important to track the process over time and compare the results to the baseline as it will help identify further improvement opportunities and ensure that the process continues to deliver the desired outcomes.
By adopting process optimization, organizations can achieve significant benefits, including increased efficiency, reduced waste, improved quality, increased customer satisfaction, reduced costs, and increased revenue.
Process Optimization Skills
- Technical knowledge: We bring a deep understanding of the process optimization methodologies, tools, and techniques and use process mapping and other related tools to identify and eliminate inefficiencies.
- Analytics: We bring the analytical skills to gather, interpret, and analyze data to understand the current process and identify areas of improvement then use that data to develop actionable insights and recommendations.
- Project management: We bring project management skills to plan, execute, and monitor the process optimization project. We set clear goals, manage timelines, and coordinate with different stakeholders to ensure the project stays on track.
- Communication: we have excellent communication skills to interact with different stakeholders in the organization and clearly explain the process optimization project’s goals, benefits, and recommendations to staff and other stakeholders.
- Change management: We use our change management skills to effectively manage the change associated with process optimization. We are also able to identify potential resistance to change and develop strategies to overcome it, this is probably the most difficult aspect of any project.
- Problem-solving: We are problem solving skills to identify the root cause of inefficiencies and develop effective solutions. We also bring out the ability to think creatively and propose innovative solutions to complex problems in collaboration with your staff.
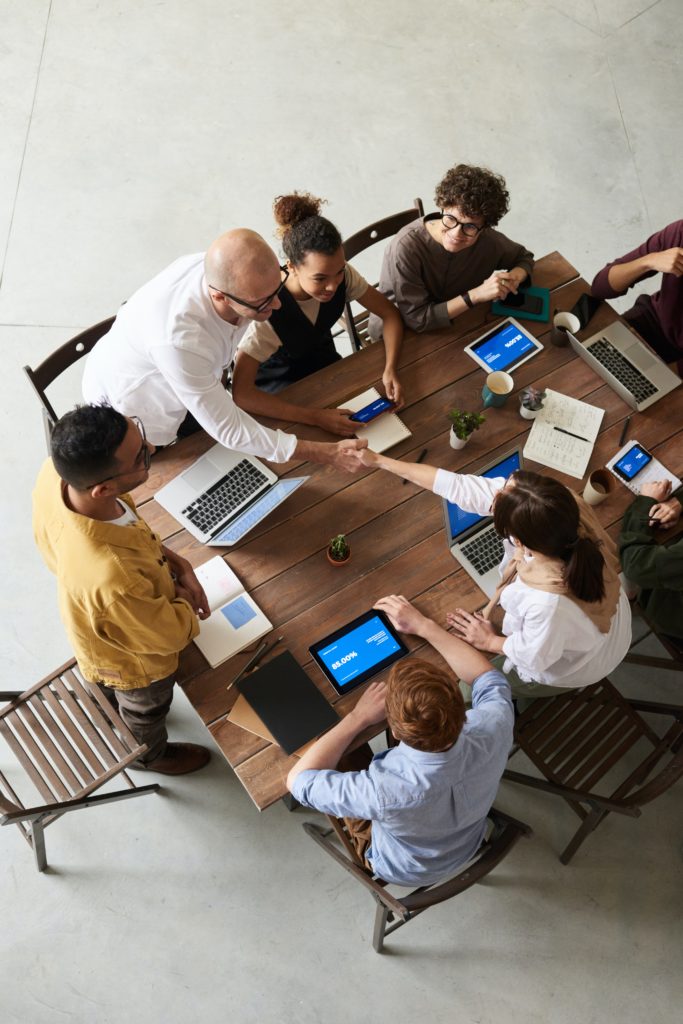
Work Examples
Service Management
- Goal: Reduce stress and overtime required of service managers.
- Result: Optimized several processes, rewrote responsibilities, and designed new analytics. The effect was a 40% decrease in workload by and a 25% increase in customer satisfaction.
Human Resources
- Goal: Optimize the on-boarding process that had not changed in over a decade during several acquisitions.
- Result: reduced a 2-week process to 1-day, aligned across all business units globally, developed a web-based solution that accounted for business unit variation, and designed a new career path for non-management staff.
Ready to explore how Process Optimization can help you? Select the link below to start the discussion.